In the demanding environment of industrial manufacturing, maintaining the reliability of critical machinery is paramount. One such vital component is the main drive gearbox, which plays a crucial role in ensuring smooth operations. We recently undertook the task of rebuilding an SRM gearbox for a tube manufacturing plant. This project involved not only precision inspections and careful reassembly but also overcoming challenges like aged components and the need for custom parts.
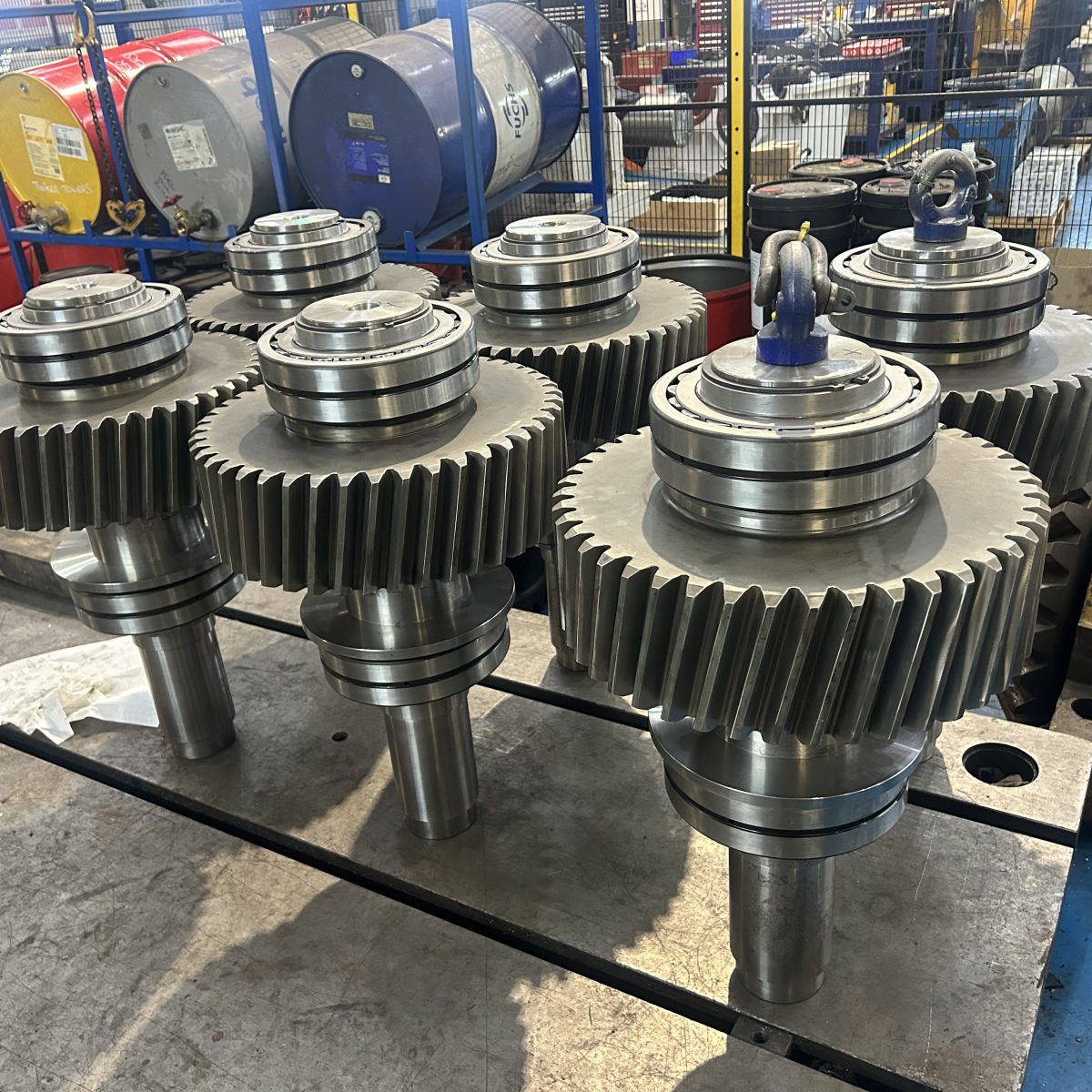
In a recent project, we undertook the rebuild of a key component of the main drive gearbox for a tube manufacturing plant. This gearbox plays a crucial role in ensuring smooth and efficient operation of the plant’s machinery, and the rebuild process required meticulous attention to detail.
The client provided us with all the necessary gearbox internals, including a brand-new casing. The casing was thoroughly inspected using CMM (Coordinate Measuring Machine) technology to ensure it met the required precision standards. Additionally, the free-issued gears and shafts were subjected to detailed dimensional inspections prior to assembly. All inspection work was carried out in-house by our experienced team, ensuring that each part met the highest quality standards before proceeding with the rebuild.
One challenge we faced was that many of the provided parts had been in the plant’s stores for several years and showed signs of corrosion and rusting. To address this, we employed techniques such as soda blasting to clean and prepare the components for assembly. This cleaning process helped restore the parts, removing contaminants while maintaining their integrity.
To ensure proper assembly, we also had to manufacture a range of spacers, which were critical for controlling axial clearances within the gearbox. These spacers were essential for correctly positioning the mating components and ensuring they fit together as intended. With the spacers in place, the assembly process could proceed smoothly.
During the build, we carefully recorded gear contact patterns and backlash measurements. This step is crucial in ensuring the gears mesh correctly and that the gearbox will run smoothly once reinstalled in the plant. Our attention to detail during this phase is critical for minimizing operational issues and ensuring the longevity of the gearbox once it is back in service.
By combining expert inspection, careful preparation, custom fabrication, and thorough testing, we were able to rebuild the SRM gearbox to the exact specifications required, ensuring that it will perform reliably in the demanding environment of the tube manufacturing plant.