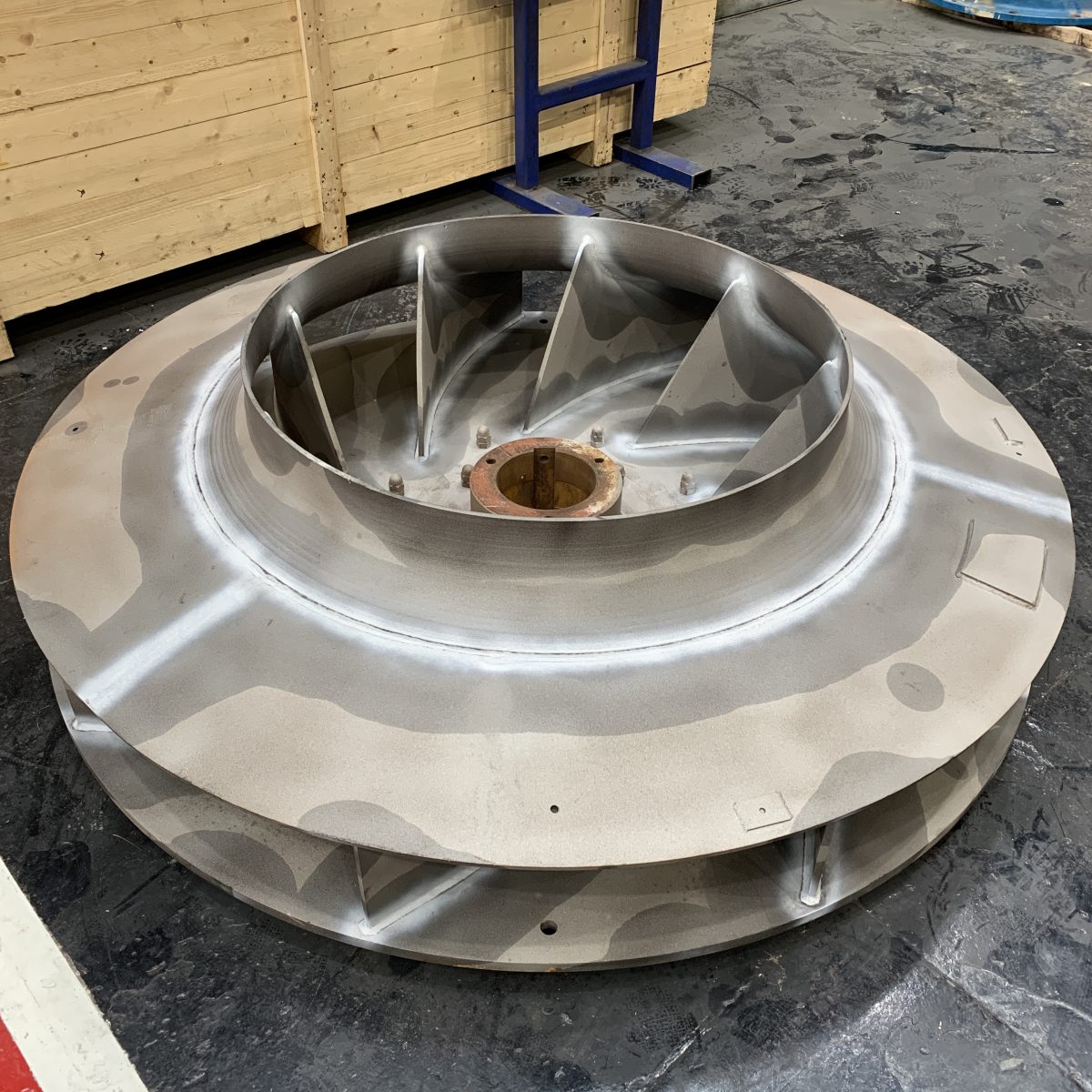
In a recent project for the recycling industry, large industrial ID fans with a 2-meter diameter underwent a comprehensive overhaul to restore their functionality and extend their operational life. Here’s a breakdown of the process:
Initial Inspection and Preparation
The overhaul began with a complete strip-down of the fans, followed by a thorough inspection and shot blasting of all components to remove debris and prepare the surfaces for repair and coating.
Non-Destructive Testing (NDT) and Repairs
Both the fan components and shafts were subjected to NDT to identify any structural flaws. Necessary weld repairs were carried out on the fans, while the shafts received additional attention, including weld reclamation of the bearing and seal journals.
Replacement of Key Components
To ensure optimal performance, the plummer block bearing assemblies were replaced with new units designed to handle the demanding operational conditions of the recycling industry.
Protective Coating Application
The fans were coated with Belzona 1331, a high-performance product known for its exceptional resistance to erosion and corrosion, providing a durable layer of protection in harsh industrial environments.
Dynamic Balancing
After repairs and coating, the fans were dynamically balanced at 1500rpm to ensure smooth and efficient operation, reducing the risk of vibrations and wear during use.
Reassembly and Delivery
With all repairs and upgrades completed, the fans were carefully rebuilt and dispatched to the client, ready to resume their role in the recycling process.
This meticulous overhaul process highlights the importance of regular maintenance and high-quality repairs for industrial equipment, ensuring longevity and efficiency in demanding applications like recycling.