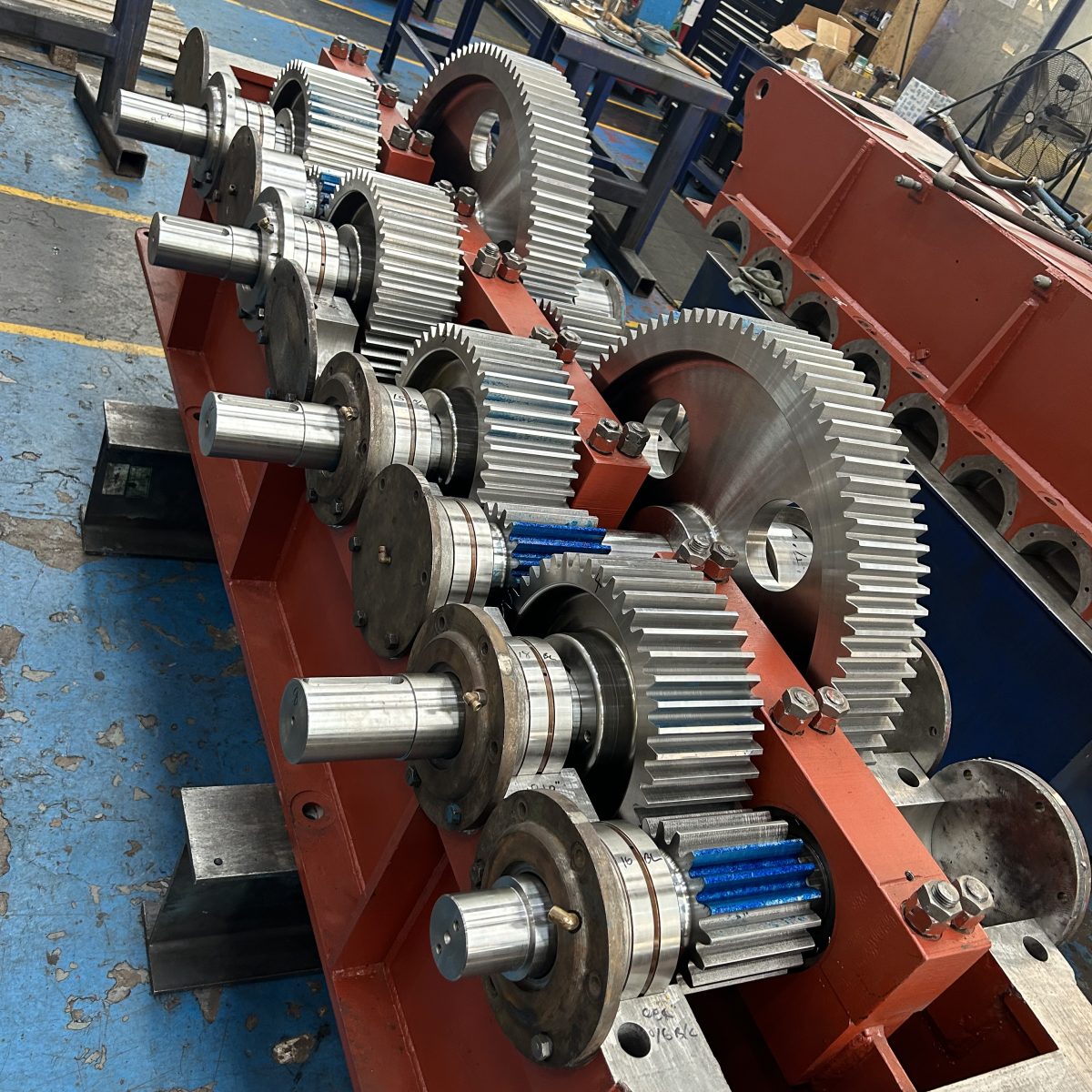
The scope of the works is as followed
- Gearbox arranged and collected directly from customers site
- Gearbox striped, inspected then reported the findings, Ensuring the reliability and longevity of gearboxes in various applications
- Shot blast gearbox casing and then performed crack detection on casing
- Prime and painted the gearbox casing internally & externally after crack detection
- Sleeve reclaim 4 off gearbox casing bores to bring them back to bearing tolerance
- Manufacture 3 off replacement end covers
- Manufacture 4 off replacement output shafts and accommodating locknuts
- Installed a new upgraded oil lubrication system, ensuring efficiency, reduce maintenance needs, enhance machine performance, and ultimately extend the lifespan of the unit
- Removing and replacing sections or the entire network of pipes responsible for delivering lubricants (such as oil or grease) to different parts of the unit
- Removal, selection, and installation of new fasteners to ensure the mechanical integrity and safety of the unit
- Supply new coupling pins & buffers for 4x output couplings, and 1x input coupling
- Supplying a complete set of new bearings and seals for the gearbox
- Machining, treating, assembling, and inspecting gears to ensure they perform reliably within a mechanical system
- Restoring and overhauling the whole unit, ensuring it is cleaned, inspected, and reassembled to ensure reliable and efficient performance
- Testing then running to ensure the proper functioning of both the gearbox and its lubrication system
- Clean down, paint, and badge, ensuring that the unit is both functional and visually appealing, with proper identification and protection for its intended use
- Transporting the fully prepared unit directly to its operational location